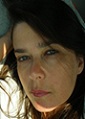
Paola Castaldo
CEO of Fastissues srls. Naples, Italy.
Title: Modeling of 3D additive manufactured nanocomposite scaffolds
Biography
Biography: Paola Castaldo
Abstract
Statement of the Problem: As bone tissue engineering is concerned, a scaffold has to provide a suitable mechanical function in order to withstand loads and to transfer the stress to the hosting tissue. Polymer-based based composite scaffolds can be processed through the additive manufacturing approach (e.g. FDM) in order to design custom made scaffolds. The purpose of this study is to analyze the stress distribution into a 3D nanocomposite scaffold according to a compressive state of stress.
Methodology & Theoretical Orientation: Cylindrical Polycaprolactone/nano-Hydroxyapatite 80/20w scaffolds were biomanufactured through a 3D plotter dispensing machine (Envisiontec GmbH, Gladbeck, Germany) at pressure of 8.5 bar and a temperature of about 120°C. Compression tests were carried out with an INSTRON 5566 at a rate of 1 mm/min. Finite element modelling (FEM) was carried out through the ANSYS software. The representative 3D scaffold design is shown in Figure 1A. The Young’s modulus and the Poisson’s ratio were set at 650MPa and 0.35, respectively. The mesh of a single unit of the cylindrical scaffold consisted of 397113 SOLID186 elements (Figure 1B).
Findings: As the scaffold undergoes a compression load, the compressive stress is mainly transferred through the regions where the plotted fibers cross each other and through part of the round boundary. Moreover, a tensile state of stress is clearly evident on the regions of fibers close to the crossing points (Figure 1C). FEM simulations are in a good agreement with the experimental results as suggested by Figures 1D.
Conclusion & Significance: FEM simulation in conjunction with experimental testing represent a very powerful tool to design custom made scaffolds.